Forschungsnetzwerk Industrie und Gewerbe
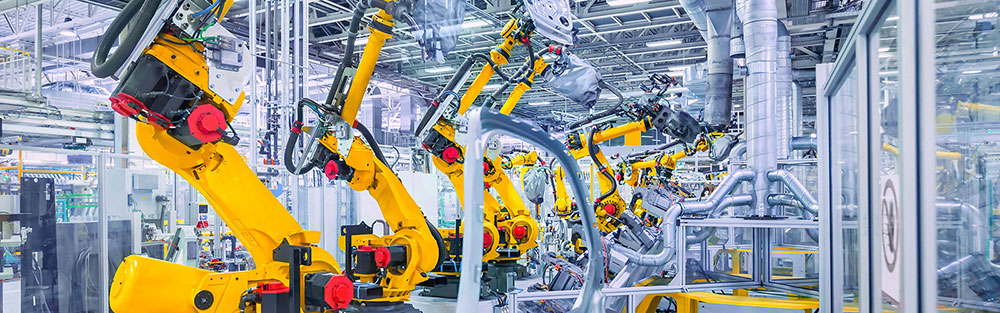
Im Forschungsnetzwerk Industrie und Gewerbe tauschen sich Expertinnen und Experten rund um die Energieeffizienz in Industrie und Gewerbe aus. Sie geben dem Bundesministerium für Wirtschaft und Energie Impulse für künftige Förderstrategien, bündeln Schlüsselthemen und liefern mit ihrer breit gefächerten Expertise innovative Konzepte und Ideen für den Erfolg der Energiewende.
Die Mitglieder des Netzwerks erarbeiten Forschungsroadmaps, Positions- und Strategiepapiere und machen damit die Fortschritte und Innovationen im Bereich Industrie, Gewerbe, Handel und Dienstleistungen (IGHD) transparent. Unter dem Dach des Forschungsnetzwerks finden die Aktivitäten der Akteurinnen und Akteure in den Forschungsfeldern Thermoprozesstechnik, Wärme und Abwärme, Wärmepumpen und Kältetechnik, chemische Verfahrenstechnik, Fertigungstechnik, Hochtemperatursupraleitung und Tribologie statt. Die Struktur der Forschungsfelder erlaubt für diese ausgewählten Schlüsselthemen eine schlagkräftige Forschung. Gleichzeitig sind die Forschungsfelder flexibel, um auch innovative Einzelthemen zu berücksichtigen. Die zunehmende Bedeutung disziplinübergreifender Zusammenarbeit ist entscheidend, um exzellente und praxisnahe Forschungsergebnisse zu erzielen und Deutschlands Position im internationalen Wettbewerb zu stärken.
Forschungsförderung für Energie im Bereich Industrie und Gewerbe
Der Fokus der Forschung liegt im Bereich Industrie und Gewerbe auf innovativen, effizienten sowie flexiblen Prozessen und Technologien, die den Energieeinsatz reduzieren. An vielen Stellen sind die Entwicklungen zur energetischen Optimierung einzelner Maschinen und Prozesse mittlerweile nahezu ausgereizt. Deshalb sind gesamte Prozessketten in Herstellungsverfahren sowie das energetische Zusammenspiel vom Rohstoff bis zum fertigen Produkt ein Schwerpunkt von Forschung und Entwicklung. Auch sekundäre Energieformen in Industrieprozessen energetisch effizient einzusetzen, gehört mit dazu. Zum Beispiel existieren im Bereich der industriellen Prozesswärme aufgrund der Vielzahl an Branchen und Prozessen bisher nahezu keine übergreifenden Konzepte. Forscherinnen und Forscher arbeiten zunächst an individuellen Wegen, die benötigte Wärmeenergie in einem bestimmten Prozess bei gleichbleibender Produktqualität zu senken. In einem nächsten Schritt sollen diese Ergebnisse in die Anwendungsbreite der Branchen übertragen werden.
Das Forschungsnetzwerk Energie in Industrie und Gewerbe hält unterschiedliche Netzwerkstrukturen für einen effektiven Austausch in der Vielfalt der Themen bereit. Schlüsselthemen, die einen langfristigen und verlässlichen Förderrahmen für eine strategische Zusammenarbeit von Forschungsgruppen benötigen, werden in sogenannten Forschungsfeldern gebündelt. Für Querschnittsthemen und für Themencluster wird die Kooperation in anlassbezogen einberufenen Veranstaltungen organisiert.
Forschungsfelder im Forschungsnetzwerk Industrie und Gewerbe
Die chemische Verfahrenstechnik beschäftigt sich mit Prozessen, in denen Stoffe nach Art, Eigenschaft und Zusammensetzung verändert werden. Die Akteure im Forschungsfeld chemische Verfahrenstechnik tauschen sich etwa zu neuen Reaktorkonzepten aus, die eine kontinuierliche und energieeffiziente Betriebsweise der Prozesse in den Anlagen ermöglicht. In der Praxis werden unterschiedlichste Prozesse nacheinander abgearbeitet – in sogenannten Chargen. Diese Batchprozesse machen die Produktion diskontinuierlich und eine exakte Regelung der Kinetik sowie der Energierückgewinnung schwierig. Die Forscherinnen und Forscher entwickeln modulare Anlagen, die Produktionsabläufe flexibler machen und neue Prozesse schneller integrieren. Damit modulare Anlagen wirtschaftlich erfolgreich werden, ist eine einheitliche Datenstruktur unerlässlich. Sie ermöglicht eine Kommunikation zwischen den Modulen und eine Dokumentation über den gesamten Lebenszyklus. Die Effizienzvorteile der Digitalisierung industrieller Prozesse können aber nur erschlossen werden, wenn die Sensorelemente auch richtige und valide Daten liefern.
Ansprechpartner/in
Dr. Kathrin Rübberdt
E-Mail: kathrin.ruebberdt@dechema.de
Website: DECHEMA - Gesellschaft für Chemische Technik und Biotechnologie
Dr. Michael Gahr
E-Mail: m.gahr@ptj.de
Website: Projektträger Jülich
Im Forschungsfeld Fertigungstechnik richten die beteiligten Akteure den Blick auf die energetischen Zusammenhänge in Prozessketten, um auch dann noch wirkungsvolle Effekte zu erzielen, wenn die Optionen zur Optimierung von Einzelprozessen ausgeschöpft sind. Die Wissenschaftlerinnen und Wissenschaftler entwickeln Lösungen, wie Maschinen untereinander, aber auch mit der Gebäudetechnik und der Gebäudehülle vernetzt werden können, sodass Energie optimal genutzt und eingespart werden kann. Für eine verbesserte Energieeffizienz in der Fertigung, beschäftigen sich Forschung und Entwicklung künftig auch mit der Integration weiterer Schlüsseltechnologien wie beispielsweise der Nano-, Kunststoff- oder Bioverfahrenstechnik. Additive Fertigung – besser bekannt als 3D-Druck – wird die industrielle Wertschöpfungskette verändern und gehört zu den Herausforderungen in der Fertigungstechnik. Im Gegensatz zu den subtraktiven und formativen Verfahren erlauben additive Fertigungsverfahren die Herstellung komplexer Geometrien und innerer Strukturen auf Basis einer schichtweisen Konstruktion.
Ansprechpartner
Prof. Matthias Weigold
E-Mail: m.weigold@ptw.tu-darmstadt.de
Website: Technische Universität Darmstadt - Institut für Produktionsmanagement, Technologie und Werkzeugmaschinen
Dr. Dmitri Tabakajew
E-Mail: d.tabakajew@ptj.de
Website: Projektträger Jülich
Ein Hochtemperatursupraleiter (HTSL) kann den elektrischen Strom nahezu verlustfrei übertragen und besitzt eine 10 bis 100 mal so hohe Stromtragefähigkeit wie ein Kupferdraht mit vergleichbaren Dimensionen. HTSL kann sowohl in der Energietechnik, bei speziellen Industrieanwendungen, als auch in modernen Stromnetzen vielfältig verwendet werden und trägt dazu bei, die Effizienz des gesamten Energiesystems zu erhöhen. Hohe Ströme bis hin zu hunderten Kiloampere kommen in Elektrolyseanlagen der Grundstoffindustrie zum Einsatz – etwa für die Herstellung von Chlor, Kupfer oder Aluminium. Wenn diese Ströme künftig durch kompakte supraleitende Hochstromschienen geleitet werden, entfallen die erheblichen Energieverluste durch den elektrischen Widerstand. Rotierende Maschinen, wie Motoren und Generatoren, können bei gleichen Abmessungen leistungsstärker und energieeffizienter ausgelegt werden. Selbst im oberen Bereich des Leitungsspektrums elektrischer Generatoren mit sehr gutem Wirkungsgrad ermöglicht die HTSL-Technologie, diesen um die letzten Zehntelprozentpunkte zu steigern.
Ansprechpartner/in
Prof. Dr.-Ing. Christof Humpert
E-Mail: christof.humpert@th-koeln.de
Website: Technische Hochschule Köln - Institut für Elektrische Energietechnik (IET)
Ralf Egen
E-Mail: r.egen@ptj.de
Website: Projektträger Jülich
Linda Hoff
E-Mail: l.hoff@ptj.de
Website: Projektträger Jülich
Viele Prozesse, die bei Temperaturen oberhalb 1.000 Grad Celsius ablaufen, werden heute mit Brennern auf Basis von fossilen Energieträgern betrieben. Die hohen Temperaturen sind bei der Herstellung von Glas, Keramik, Ziegeln und Metallen ebenso notwendig wie bei Zement und in weiteren Branchen. Um den Energieverbrauch zu reduzieren, sollen die Prozesstemperaturen und damit der Brennstoffbedarf gesenkt werden — dies kann etwa durch eine genauere Prozessführung an den Grenzen der technisch notwendigen Temperaturfenster gelingen.
Ziel ist es zudem, die Prozesse zu defossilisieren und Brennstoffe wie Erdgas und Kohle vollständig zu ersetzen. Sofern dies technisch möglich ist, können einige Prozesse zukünftig mit klimaneutralem Strom elektrisch beheizt werden. Eine weitere Alternative ist der Umstieg auf klimaneutrale Brennstoffe. Aus wirtschaftlichen Gründen kann dieser auch im Sinne einer Übergangstechnologie und schrittweise gestaltet werden. In allen Fällen entsteht Bedarf für Forschung und Entwicklung: bei der Anpassung der Wärmeerzeugung, des Wärmeeintrags und der Prozessführung.
Das neue Forschungsfeld Thermoprozesstechnik geht durch Erweiterung des Themenzuschnitts aus dem ehemaligen Forschungsfeld Metallerzeugung und -verarbeitung hervor.
Ansprechpartner
Dr. Joachim Wünning
E-Mail: j.g.wuenning@flox.com
Website: WS Wärmeprozesstechnik GmbH
Dr. Ralph Edenhofer
E-Mail: r.edenhofer@ptj.de
Website: Projektträger Jülich
Dr. Erik Skiera
E-Mail: e.skiera@ptj.de
Website: Projektträger Jülich
Tiefgehende Kenntnisse aus Physik, Chemie sowie verschiedensten Ingenieurwissenschaften sind nötig, um die Vielfalt der Phänomene rund um die Vorgänge Reibung, Verschleiß und Schmierung zu verstehen und damit umfassend optimieren zu können. Daher ist die Vernetzung mit anderen Forschungsschwerpunkten essenziell. Den größten Einfluss auf einen tribologischen Kontakt zwischen den Reibpartnern hat ein Schmierstoff, denn über ihn lassen sich bestimmte Faktoren eingrenzen. So werden in Forschung und Entwicklung zum Beispiel neue Werkstoffe beziehungsweise Beschichtungsmaterialien entwickelt und mit Tribometern systematisch auf ihre Eignung untersucht. Die Tribologieforschung zeigt, dass etwa eine Maschine mit unterschiedlichen Reibpaarungen systemisch betrachtet und einen globalen Lösungsansatz benötigt. Für die Forscherinnen und Forscher gewinnen in diesem Zusammenhang Digitalisierung und Künstliche Intelligenz, neue Technologien zur Datenerfassung sowie die Nutzung modernster Methoden der Datenauswertung zum Verständnis tribologischer Daten eine immer größere Bedeutung.
Ansprechpartner
Dr.-Ing. Thomas Lohner
E-Mail: thomas.lohner@tum.de
Website: Technische Universität München - Lehrstuhl für Maschinenelemente
Dr. Michael Gahr
E-Mail: m.gahr@ptj.de
Website: Projektträger Jülich
Dr. Stefan Busse-Gerstengarbe
E-Mail: s.busse-gerstengarbe@ptj.de
Website: Projektträger Jülich
Bei nahezu jedem industriellen Prozess entsteht Wärme. Das reicht von vergleichsweise niedrigen Temperaturen von rund 40 Grad Celsius, die in der Industrie bei technischen Anlagen wie etwa Kompressoren oder Pumpen entstehen, bis zu über 1.000 Grad Celsius bei Verbrennungsprozessen. Abwärme kann direkt als Wärme für Folgeprozesse auf niedrigeren Temperaturniveaus genutzt werden. Eine indirekte Nutzung ist möglich, wenn die Wärme etwa mit Thermoelektrik oder Organic-Rankine-Cycle in Strom gewandelt oder mittels effizienter Wärmepumpen aufgewertet und in Hochtemperaturprozesse zurückgespeist wird. Bei allen Anwendungen sind Wechselwirkungen und Zusammenhänge zwischen Wärmequellen, Wärmesenken und thermischen Speichern sowie die Rückwirkungen oder Netzdienstleistungen auf das Energiesystem zu betrachten.
Ansprechpartner
Dr. Andreas Hauer
E-Mail: andreas.hauer@zae-bayern.de
Website: ZAE Bayern Bayerisches Zentrum für Angewandte Energieforschung, e. V
Dr. Stefan Busse-Gerstengarbe
E-Mail: s.busse-gerstengarbe@ptj.de
Website: Projektträger Jülich
Marina Zingsheim
E-Mail: m.zingsheim@ptj.de
Website: Projektträger Jülich
Wärmepumpen sind eine Schlüsseltechnologie für die klimaneutrale Beheizung von Gebäuden. Sie erschließen Umweltwärme, heben diese Energie mit geringen Mengen von zukünftig grünem Strom auf ein höheres Temperaturniveau an und transportieren sie ins Gebäudeinnere. Im Zuge der Wärmewende ist zu erwarten, dass Wärmepumpen in hohen Stückzahlen und in prinzipiell ähnlichen Einbausituationen zum Einsatz kommen werden. Es bestehen somit hohe Anreize dafür, die Komponenten, Geräte und Anlagen sowie ihre Fertigung weiter technisch zu optimieren — da so der Energieverbrauch gesenkt und die Wirtschaftlichkeit erhöht werden kann.
Industriewärmepumpen für höhere Temperaturen sind dagegen noch nicht weit verbreitet. Ein Hemmnis für ihre wirtschaftliche Anwendung ist, dass die Effizienz der Wärmepumpe entscheidend davon abhängt, dass sie optimal an die verfügbaren Wärmequellen und Wärmesenken angepasst ist. Dazu muss sie individuell in die vorgefundene Prozesstechnik integriert werden. Forschungsbedarf besteht neben der Entwicklung von Komponenten und Geräten also auch darin, die Integration zu vereinfachen.
Ansprechpartner
Dr.-Ing. Marek Miara
E-Mail: marek.miara@ise.fraunhofer.de
Website: Fraunhofer ISE
Steffen Linsmayer
E-Mail: s.linsmayer@ptj.de
Website: Projektträger Jülich
Wie tragen Künstliche Intelligenz, Sensorik, Aerogele oder Wide-Bandgap-Halbleiter zur Energieeffizienz bei?
Einige Querschnittsthemen treten als Arbeitspakete in sehr vielen Förderprojekten auf. Sie sind daher auch im Forschungsnetzwerk Industrie und Gewerbe wichtiger Bestandteil von Diskussionen und gemeinsamer Forschung. Unter dem Oberbegriff Digitalisierung in der Produktion bildet innovative Sensorik die Voraussetzung für immer feinere Daten über Prozesszustände, mit denen Energieverluste erkannt und effiziente Steuerungen möglich werden. Hierbei kommen zum Teil auch Methoden der künstlichen Intelligenz zum Einsatz.
Aerogele und Halbleiter mit breitem Bandabstand (sogenannte Wide-Bandgap-Halbleiter, kurz: WBG-Halbleiter) sind zwei weitere Beispiele für aktuelle Themencluster, in denen Forscherinnen und Forscher über mehr als eine Förderperiode hinweg kooperieren und sich intensiver mit innovativen Materialien und Verfahren beschäftigen.
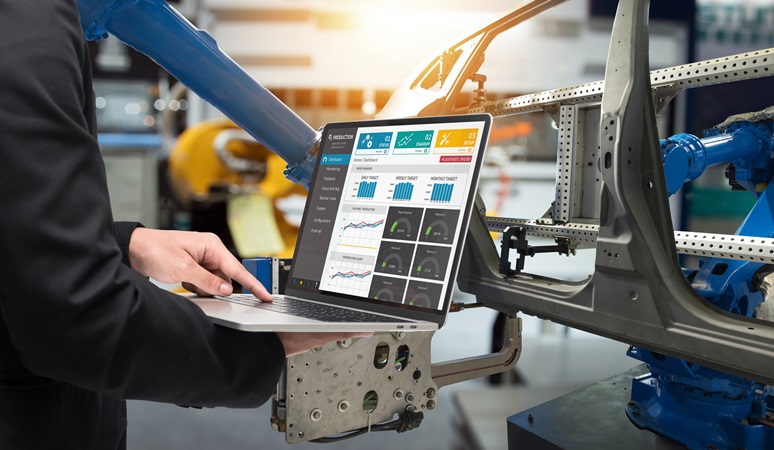
Begleitforschung Industrie und Gewerbe
Die Begleitforschung EE4InG 2 ist eng mit den Forschungsfeldern des Forschungsnetzwerks Industrie und Gewerbe verzahnt. Gemeinsam mit den Mitgliedern des Netzwerks identifiziert sie Lösungen in Forschung und Entwicklung, die das Potenzial haben, die Energieeffizienz im Bereich Industrie und Gewerbe zu steigern.
Ein zentrales Projektziel ist die wissenschaftliche Querauswertung der angewandten Energieeffizienzforschung und der Förderung durch das Energieforschungsprogramm des BMWE im Hinblick auf Vergangenheit, Gegenwart und Zukunft. Zudem will das Team der Begleitforschung den Austausch zwischen relevanten Akteurinnen und Akteuren des Innovationssystems (Industrie, Wissenschaft, Politik) stärken. Dies wird insbesondere durch verschiedene Austauschformate und Veranstaltungen — wie etwa dem Industriewende-Dialog — sowie durch die Koordinierungsstelle des Begleitforschungsprojekts unterstützt.
Das Begleitforschungsprojekt EE4InG 2 startete im November 2023 und läuft über vier Jahre. Koordiniert wird das Projekt vom Institut für Ressourceneffizienz und Energiestrategien (IREES). Weitere Partner sind das Institut für Industrieofenbau und Wärmetechnik (IOB) der RWTH Aachen, sowie ETA-Solutions, eine Ausgründung der TU Darmstadt. Die Begleitforschung EE4InG 2 wird ihre Forschungsergebnisse in mehreren Publikationen veröffentlichen.
EE4InG 2 knüpft an die inhaltlichen Vorarbeiten des vorausgegangenen Begleitforschungsprojekts EE4InG an. Dieses startete im Oktober 2018 und endete nach einer Projektlaufzeit von drei Jahren im Herbst 2021. Auch die Begleitforschung EE4InG hat ihre Forschungsergebnisse in mehreren Publikationen veröffentlicht.
Kurzstudie EE4InG2
Das Team des Begleitforschungsprojekts EE4InG 2 hat im Sommer 2024 eine Kurzstudie zur Relevanz der öffentlichen Energieforschungsförderung mit dem Fokus auf Industrie und Gewerbe veröffentlicht. Die Studie erreichen Sie über die Webseite der Begleitforschung EE4InG 2 oder alternativ über den Button.
Direktlink zur Kurzstudie von EE4InG 2